A Lean Warehouse is created through lean management tools and techniques. This article outlines the results available through Lean Management and the tools used to achieve these lean results.
Implementing Lean warehouse principles is essential for optimizing efficiency, reducing waste, and improving overall productivity in logistics and supply chain operations. This comprehensive list of Lean warehouse tools provides a structured approach to streamlining workflows, enhancing quality, and fostering a culture of continuous improvement. From 5S organization and Kanban systems to Just-in-Time (JIT) inventory management and value stream mapping (VSM), these proven methodologies help warehouses minimize delays, reduce excess inventory, and maximize space utilization. By incorporating automation, visual management, and employee empowerment strategies, businesses can create a more agile, cost-effective, and customer-focused warehouse environment. Whether you’re looking to improve order fulfillment speed, warehouse safety, or inventory accuracy, these Lean tools offer practical solutions to drive long-term success and operational excellence.
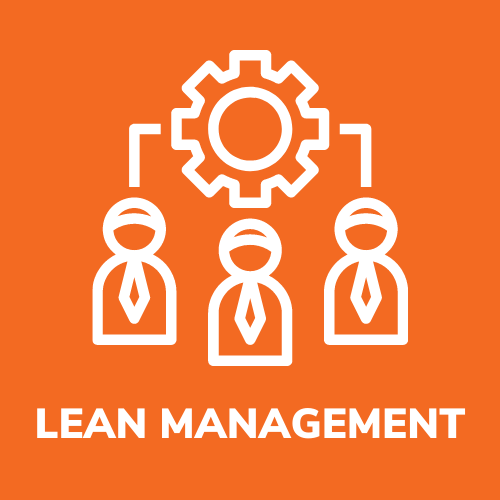
Read below to learn more about lean management tools and best practices.
Lean Management produces these results
- Improved work productivity, and efficiency
- Reduced cost by eliminating waste
- Safer work environment
- Improved quality
- More environmentally-friendly work practices
- Increased in profitability
- Customer and employee satisfaction
Lean Warehouse Tools to achieve a lean work-place include:
Workplace Organization & Standardization
- 5S – A workplace organization system designed to improve efficiency and eliminate waste. It consists of:
- Sort (Seiri) – Removing unnecessary items.
- Set in Order (Seiton) – Organizing essential items for easy access.
- Shine (Seiso) – Cleaning the workplace to maintain a safe and productive environment.
- Standardize (Seiketsu) – Establishing rules and best practices to maintain the first three steps.
- Sustain (Shitsuke) – Ensuring long-term adherence through audits and continuous improvement.
- Standardized Work – The systematic documentation of every work element and process step for each operation. Standardization ensures consistency, efficiency, and easier identification of improvement opportunities.
- Visual Management – Using signs, floor markings, screens, and color codes to communicate important information instantly.
- Ergonomics & Safety Integration – Designing workstations and processes to reduce worker fatigue, enhance safety, and improve productivity.
Process Efficiency & Flow
- Kanban System – is the process of continuous delivery to help teams work together more effectively. By using visual cues, invisible work is made visible, helping with its management. The visual workflow management tool ensures a smooth, just-in-time flow of materials and tasks. It helps teams visualize work in progress, limit overproduction, and enhance efficiency.
- Leveled Production (Heijunka) – Balancing warehouse operations to match inbound shipments with outbound order fulfillment, reducing inefficiencies.
- One-Piece Flow – Ensuring each order or task moves through the lean warehouse without delays or work-in-process (WIP) accumulation.
- Just-in-Time (JIT) Inventory Management – Minimizing excess inventory by ensuring materials and products arrive only when needed, reducing storage costs and waste.
- Pull System – Replenishing inventory only when required rather than pushing stock based on forecasts, reducing overproduction.
- Cross-Docking – A logistics method where inbound shipments are immediately transferred to outbound trucks with minimal storage time.
- Quick Changeover (SMED – Single-Minute Exchange of Die) – Reducing the time needed to switch from one task or product to another, minimizing downtime.
Waste Identification & Elimination
- Waste Elimination (Muda) – Removing non-value-added activities. Lean identifies seven types of waste:
- Overproduction
- Waiting/Delays
- Unnecessary Transportation
- Overprocessing
- Excess Movement
- Excess Inventory
- Defects/Rework
- Right-Sizing Equipment & Storage – Ensuring warehouse equipment and storage configurations are optimized to maximize space utilization and efficiency.
- Mistake-Proofing (Poka-Yoke) – Implementing fail-safes to prevent errors before they happen through visual cues, automated alerts, or standardized procedures.
- Spaghetti Diagram – A mapping tool to visualize and reduce unnecessary physical movement in warehouse workflows.
- Streamlining Processes – Simplifying and optimizing warehouse workflows to eliminate inefficiencies, reduce unnecessary steps, and improve overall productivity.
- Value Stream Mapping (VSM) – A Lean tool used to analyze and improve the flow of materials and information. It visually maps the current state, identifies inefficiencies, and designs an optimized future state.
Quality & Continuous Improvement
- Continuous improvement (Kaizen) – A cultural mindset where learning, action, problem recognition, problem-solving, and quick adjustments drive everyday operations. Businesses must learn to allow for learning while doing. This means, action, problem recognition, problem-solving, and quick adjustments must form the basis of business activity.
- A3 problem solving – A structured problem-solving approach developed by Toyota that follows these steps:
- Background – Why the problem needs solving.
- Current state – Identifying key data points.
- Future state – The desired outcome.
- Root cause analysis – Identifying why the problem exists.
- Countermeasures – Developing solutions.
- Implementation plan – Executing solutions.
- Follow-up – Reviewing effectiveness.
- Gemba Walks – Managers and team leaders physically visit the warehouse floor to observe operations, engage with workers, and identify improvement opportunities.
- Layered Process Audits (LPA) – Conducting routine audits at different organizational levels to ensure Lean practices are sustained.
- Kata Coaching – A structured approach to problem-solving and continuous improvement, embedding Lean thinking in daily operations.
- Empowering Workers to Ensure Quality (Andon System) – A system where employees have the authority to stop production when they detect a quality issue. Inspired by Toyota’s andon cord, this prevents defects from continuing down the line. At Toyota factories, a yellow line can be seen that runs along the assembly track, called the andon cord. Every worker is empowered to stop production on the line when an unresolved quality issue is found.
Metrics & Performance Optimization
- Takt Time – The pace at which orders must be processed to meet customer demand, helping balance workloads and prevent bottlenecks.
- Overall Equipment Effectiveness (OEE) – A performance metric that measures equipment availability, efficiency, and quality output.
- Yamazumi Chart – A stacked bar chart used to visualize workload distribution and identify process imbalances.
- Heijunka Box – A scheduling tool that visually levels workloads to maintain stable production in a warehouse environment.
- Leveled Production (Heijunka) – Balancing incoming inventory with outgoing shipments to prevent bottlenecks, reduce variability, and ensure smooth order fulfillment. Applies to both receiving and order-picking processes.
Communication & Team Engagement
- Respect people – A core Lean principle that emphasizes engaging frontline workers in process improvement. Employees at the gemba (workplace) are closest to the work and often have insights that lead to better efficiency and quality.
- Asaichi Meetings – Short morning meetings to review previous-day challenges, resolve issues, and set daily priorities, fostering accountability and teamwork.
- Hoshin Kanri (Policy Deployment) – A strategic planning method that aligns company goals with warehouse operations, ensuring long-term Lean improvements.
- Autonomation (Jidoka) – “Automation with a human touch.” This concept ensures that machines or processes halt when a defect is detected, allowing quick problem resolution without producing defective products.
- Customer-first approach – Lean warehousing prioritizes customer satisfaction by aligning processes with customer needs, reducing lead times, and ensuring accurate and timely deliveries.
Technology & Digital Lean
- Total Productive Maintenance (TPM) – A proactive maintenance strategy that reduces downtime and increases equipment efficiency.
- Digital Lean (Automation & AI Integration) – Utilizing warehouse management systems (WMS), AI-driven analytics, RFID tracking, and robotics to further streamline Lean processes.
- Reverse Logistics Optimization – Applying Lean principles to manage returns, refurbishments, and recycling in a cost-effective and efficient manner.
ADVERTISEMENT